Copy of An Overview of Hydraulic Motor Types
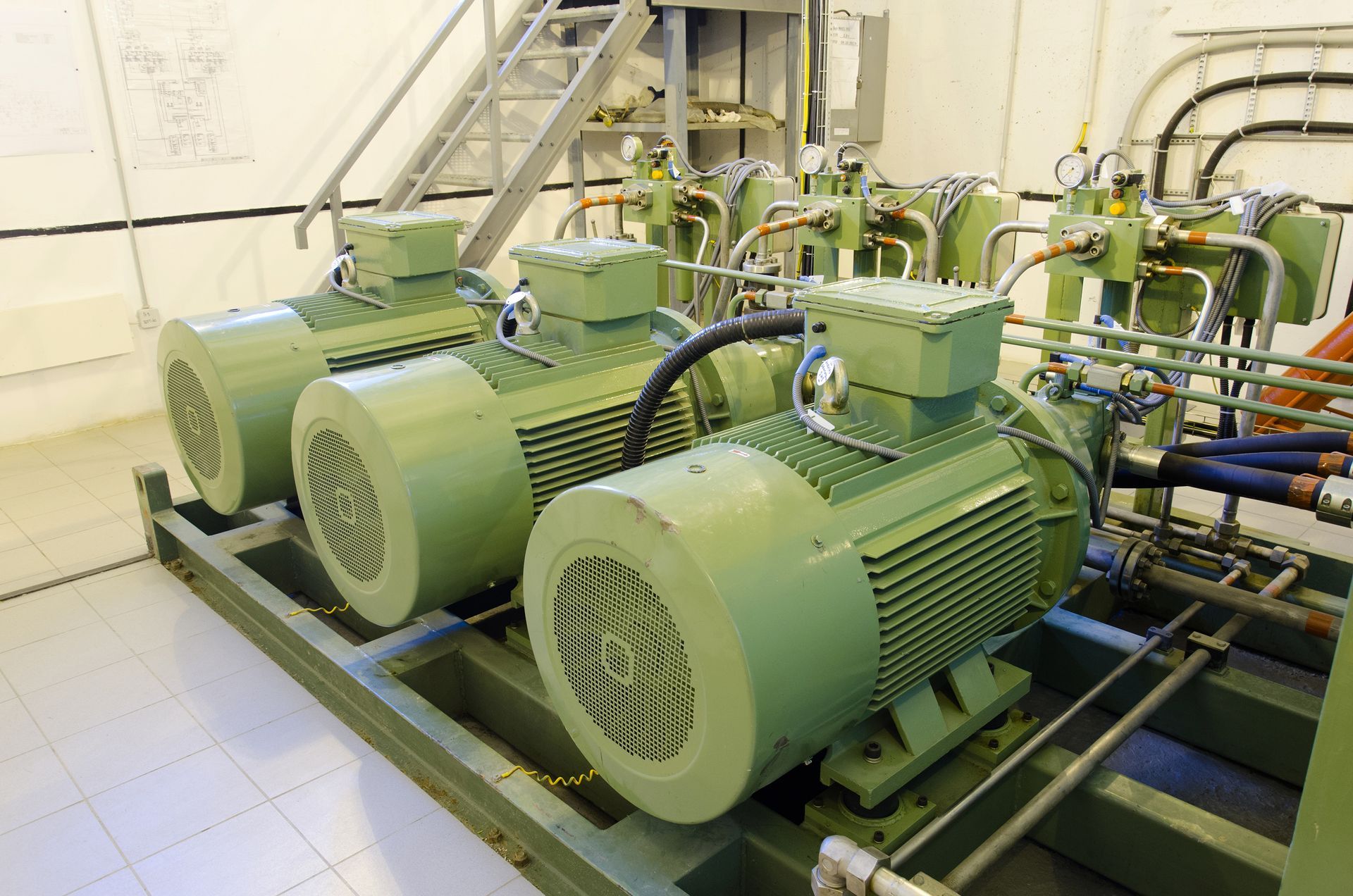
In the realm of hydraulic systems, the choice between an open loop and a closed loop configuration marks a fundamental decision that shapes the efficiency, functionality, and performance of various mechanical applications.
Understanding the distinctions between these two hydraulic system types is pivotal to making informed decisions when selecting the most suitable hydraulic setup for your specific needs. Let's delve into the world of hydraulic circuits, exploring the differences, advantages, and applications of open loop and closed loop configurations.
Open Loop System
In open loop hydraulic systems, the hydraulic pump, its motor, and actuator's input and return connections all lead back to the same reservoir of hydraulic fluid. The fluid circulates between the reservoir and the actuator. A relief valve or other pressure-regulating control valve directs the flow to the actuator before the used fluid is recycled back into the storage container.
An open loop hydraulic circuit's primary benefit is its low price. It's more efficient and cost-effective than alternatives that necessitate a closed circuit but would require more complex equipment and more power. Because of the reduced number of parts, open loop circuits are also easier to service and analyze.
However, open loop hydraulic circuits are less efficient than closed-loop ones. Since the fluid does not circulate in a closed loop, it may take a while to refill the reservoir, which may result in inefficient heat production and a decrease in efficiency. The volume of the reservoir also needs to be adequate for sufficient cooling.
Heavy machinery commonly uses open loop hydraulic systems because of their simplicity and low cost. Systems that run at lower pressures, including turbines, heat exchangers, and cranes, benefit the most from open loop control systems.
Closed Loop System
Mobile applications that require a lot of power under high pressure, such as skid steers and refrigerators, use closed loop hydraulic circuits. These systems eliminate the need for a storage tank altogether by routing fluid straight from the pump to the motor before returning to the pump via a series of valves, filters, and accumulators. This design decreases the system's overall complexity, cost, and mass.
The primary pump in closed-loop systems is typically a fixed-displacement pump with a capacity of only about 15% of that of an open-loop system's primary pump. In addition to the lower oil reservoir, this contributes to the system's reduced size and cost.
Precise motion control uses, such as those required in mobile equipment and machinery and automated manufacturing processes, are ideally suited to closed loop circuits. Closed loop systems are self-sustaining and can be utilized in more compact configurations than open loop systems because they eliminate the need for external control devices like valves to regulate fluid flow.
In a closed-loop hydraulic system, the applied pressure of the hydraulic fluid (often hydraulic oil) drives the motor. The main pump regulates the entire system's fluid pressure and flow and can change the motor's rotational direction by directing fluid via one of the two ports.
Closed loop hydraulic systems are challenging to evaluate and expensive to repair because of their reliance on precise control. These systems also require hydraulic fluid filtration at elevated pressures to protect the motor and other parts from contamination.
Bottom Line
The ideal circuit for a hydraulic system varies based on the system's design and intended purposes. Closed loop systems are suitable for wheel and track drive motors on moveable machines and mobile equipment because of their lightweight and precision. In contrast, open loop systems are ideal for systems that rely on cylinders or rotators due to their durability.
Contact us at
Quad Fluid Dynamics Inc for hydraulic pump equipment and parts.